Whether it is the food we consume, the drinks we take and the colors we have in our warehouses and stores, almost every aspect of our daily lives cannot be complete without the concept of packaging. Moving any reliable container back there is an exquisite mix of engineering, materials science as well as complex machines and equipment that guarantee durability, hygiene as well as efficiency.
Metal packaging requires perfect seams and perfect seals and shapes. Whether it’s the metal can bottom end of a soup tin or the intricate cuts on a cardboard insert, packaging components are not created at random—they are engineered with precision and purpose. At the heart of this process are machines like the semi-automatic flatbed die cutting machine, which bridges the gap between custom design and high-speed production.
This article will discuss how such technologies are coming together to create the world of containers that turn raw sheets into workable, safeguarding and aesthetically pleasing packaging solutions within different sectors.
Semi-Automatic Flatbed Die Cutting Machines: How Precision Shapes Productivity
The semi-automatic flatbed die cutting machine is a cornerstone of precision packaging manufacturing. The machine has been developed to cut, crease or emboss such materials as paperboard or corrugated board, plastic sheets or candy wrapping and even thin metals. By contrast, one difference lies in the fact that they consistently make cuts, with the utmost precision, even when the shape is complicated or custom.
Flatbed die cutting does not require rotary cutters or manual operations, as there is a stationary flatbed on which the material is laid down, and the die is pressed on it to give accurate format. The material feeding and removal are frequently manually controlled in the semi-automatic types which provide flexibility and control particularly in mid-range volumed production facilities.
Key advantages includes the following:
- Superior edge quality and dimensional accuracy
- Capability to cut intricate shapes with uniform pressure
- Reduced material waste due to precise alignment
Manufacturers value the semi-automatic flatbed die cutting machine for its balance of automation and operator oversight. It is particularly useful in industries where changeovers are frequent, or where a product is still in development; running high-value downstream packaging is when customization tactics and precision win out over automation.
Regardless of whether one is making packaging inserts, container linings, or decorations these machines make sure that the respective component is an ideally fitting component of the ecosystem that is the packaging.
Metal Can Bottom Ends: Structural Engineering for Strength and Sealability
The metal can bottom end may seem like a simple disc of tin or aluminum, but it is in fact a product of precise structural engineering. It should be able to take pressure inside, be able to seal out corrosions, and be able to fit with the body and lid of the can. The integrity of this component is not desirable in food, beverage, chemical and pharmaceutical industries.
Usually produced using tinplate, aluminum, or tin-free steel, the metal can ends are produced using a list of punching, curling and sealing procedures. The bottom end is also designed to reinforce itself, often having features such as rib, countersink or beads so that its strength is reinforced but not its weight. These aspects aid in equalizing internal pressure in pressurized containers (such as soda cans), and thus reducing the likelihood of deformation.
Modern production of metal can bottom ends involves:
- Precision stamping dies to ensure exact diameter and edge profile
- Hermetic sealing capabilities to maintain shelf life
- Coatings and lacquers for corrosion resistance and food safety compliance
From Sheet to Shape: Coordinating Cutting Technology with Metal Component Design
The efficiency of packaging lies in the coordination of materials and machines to be flawless. From flat sheets of aluminum or tinplate to fully formed metal can bottom ends, the production chain relies on a series of precisely aligned steps. This is where technologies like the semi-automatic flatbed die cutting machine interface with metal forming systems to support the overall workflow.
Examples here include applying die cutting machines upstream to cut gaskets, seals, liners as well as outer labels that would snugly fit with can components. These die cut strips are supposed to fit the cans beautifully, especially the bottom and the lid, so there can be air tight seals or there can be good bonding because of the adhesive.
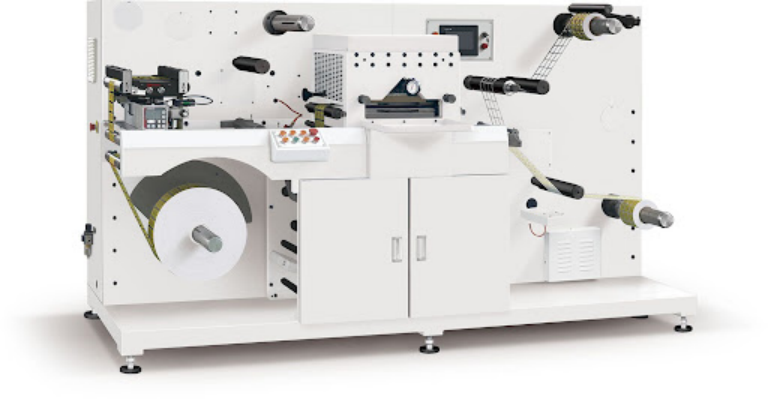
Working with metal sheets precision is very vital. Alignment on a die-cut liner or adhesive label that is off would negate the sealability or stackability of the can. Producers can connect die cutting stations within the metal stamping lines incorporating the speeds and also the feeds to ensure a constant form of just-in-time work.
Such degree of coordination entails:
- Computer-aided design (CAD) to align cutting patterns with metal part geometries
- Tight tolerances to ensure compatibility across different materials
- Quality control sensors to monitor alignment, edge finish, and fit
Applications in Food, Beverage, and Industrial Packaging Systems
The practical applications of metal can bottom ends and semi-automatic flatbed die cutting machines span a wide range of industries. Metal cans are used in the food and beverage industry to preserve most of the things including the vegetables and soups, carbonated drinks, and even the coffee. Strong and stable bottom end is important towards the security of contents during transportation and storage.
In the same token, die cutting machines play a critical role in manufacturing bespoke parts that embellish these packaging systems- including foil lids, foam liners as well as protective sleeves. Metal Containers In the pharmaceutical industry, metal containers are frequently chosen to pack products that involve high hygiene requirements, and/or barrier protection. In this case, die-cut safety seals together with tamper-proof liners should comply with metal can parts.
Adhesives, paints, oils and solvents in the industry are stored in cans. All the machining of the bottom of a can to withstand the internal chemical pressure or corrosion is of the essence as accurate as any of the die-cut inserts or external branding material that is present.
Conclusion:
Modern packaging is a masterclass in precision—every component, from the metal can bottom end to the gasket liner, must perform flawlessly. Behind this reliability are powerful tools like the semi-automatic flatbed die cutting machine, enabling high-quality, repeatable results across a range of materials.
Combined they comprise the heart of the packaging process with integrity and efficiency. As the sophisticated consumer demands increase, the combination of die-cut technology and advanced metal forming makes the products safe, fresher, and attractive than ever.