All the flowing products, including refreshing drinks and essential medicines, rely on well-coordinated systems to be produced. Among the most crucial components of liquid processing lines are the mixer tank and the filling machine. Without these unsung heroes, what finds its way into your bottle, pouch or jar is not uniform, not precisely measured and free of contamination.
The two systems are essential in the contemporary industrialized world where efficiency and uniformity are not negotiable. Mixer tanks ensure ingredients are blended to the exact texture, temperature, and concentration required. Filling machines follow through by portioning the product into packages with remarkable accuracy.
These systems are not all about automation, they are decades of engineering, physics and chemical science in harmony. This paper will discuss the working of mixing and filling systems, their synchronization, and the importance of the system in any industry, such as food and pharmaceuticals.
Mixer Tank: The Physics of Homogenization and Volume Consistency
At the heart of every fluid-based production process lies the mixer tank—an engineered vessel that blends multiple ingredients into one homogeneous mixture. However, there is more than swirling liquids together when it comes to mixing. It is a science that has to do with turbulence, shear force, heat transfer and even chemical kinetics.
A typical mixer tank is fitted with rotating impellers or paddles that create dynamic fluid movement. The configuration and the rate of these agitators is based on the viscosity and the chemical characteristics of the contents. As an example, honey based products need low speed and high torque agitation but fruit juices or cleaning chemicals need high speed and turbulence.
This is done with the aim of removing concentration gradients and getting an equal distribution of solids, liquids, or gasses across the mixture. The mixing process is usually facilitated by temperature controls, particularly where heat-sensitive products such as dairy or pharmaceuticals are involved.
Advanced mixer tanks also incorporate sensors and feedback loops to monitor mixing time, speed, and fluid volume. These tanks are usually attached to automated control panels that control every batch with repeatability. By the time the product leaves the tank, it’s ready for the next stage—packaging via the filling machine.
Filling Machine: How Automation Ensures Accuracy and Speed
Once the mixture is ready, it moves to the filling machine, where accuracy and speed are the stars of the show. These are the last machineries before products get to the consumer. Whether it’s shampoo in a bottle or cough syrup in a vial, filling machines ensure the exact volume is delivered, every time.
Filling machines operate using different mechanisms based on the type of product and container. Gravity fillers use the power of gravity to fill the bottles- suitable to thin liquids such as water or wine. Piston fillers apply cylinders to push more viscous products such as sauces or gels. The sterile applications, particularly in pharma, frequently utilize peristaltic pumps because they do not contaminate.
Modern filling machines are fully automated and often integrated with conveyor systems, nozzle arrays, and sensor-driven controls. This degree of automation guarantees high throughput, minimizes human error, and ensures hygiene, particularly in a place where strict regulatory requirements are in place.
The versatility of these machines makes them essential. They are able to fill hundreds of bottles a minute, they can process many different shapes and sizes of bottles and change between products with minimal downtime. They are very efficient, which directly converts into cost savings and improved product consistency.
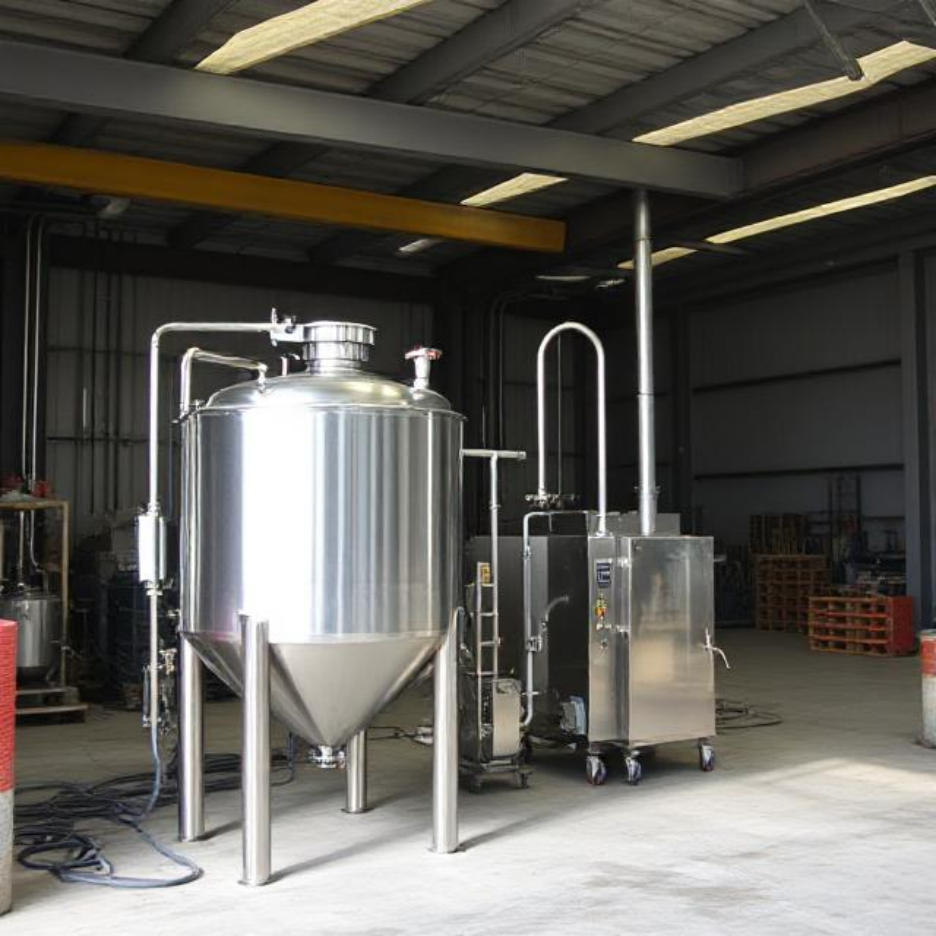
Synchronizing Mixer Tanks with Filling Machines for Seamless Operation:
Productivity does not only mean strong machines but also how well they interact. Synchronizing the mixer tank with the filling machine creates a seamless flow from blending to packaging, minimizing delays and material waste.
To begin with, a mixer tank must deliver product to the filling machine at a consistent pressure and flow rate. This must be well coordinated with automated valves, pumps and buffer tanks. If the mixer tank is empty or not ready, the filling machine must pause—or worse, it may run dry, causing errors and potential damage.
This is the reason why Programmable Logic Controllers (PLCs) and Supervisory Control and Data Acquisition (SCADA) are used in most systems to coordinate timing and data flow between the two units. These systems monitor the progress of batches, temperature, fill levels and even anomalies in real time.
Batch tracking is one of the advanced features in the modern production lines. Every mix from the tank is tagged with a batch ID, which the filling machine logs as it fills containers. This allows traceability to its fullest extent and also means that in the event of a problem the manufacturers can isolate and recall only the problematic batch which is crucial in the food and pharma industries.
Moreover, coordinated activities decrease the expenses of labor, save losses of products, and increase energy consumption. The outcome is a well-cleaned, dependable and scalable process- which is essential in the current production schedules that are more demanding.
Industrial Applications: From Beverages to Pharmaceuticals
The combination of mixer tanks and filling machines is used across a wide range of industries, each with unique demands and challenges.
These systems are used in the food and beverage sector to deal with everything, including soft drinks and soups, dressings, and dairy. Mixer tanks ensure proper ingredient dispersion and emulsification, while filling machines adapt to various packaging types like bottles, cartons, and pouches.
Precision mixing of creams, serums and gels is an advantage to the cosmetic industry as they need to be of a specific texture and consistency. Here, hygiene and product integrity are key—making clean-in-place (CIP) systems essential in both mixer tanks and filling machines.
In the case of pharmaceutical manufacturing, there is more at stake. Mixer tanks must blend active ingredients accurately under sterile conditions, while filling machines must meet regulatory requirements such as FDA, EU GMP, and USP standards. Any change in volume or contamination can be quite devastating.
These systems are even used by chemical industries in paints, cleaning agents and adhesives. Tanks designed for corrosive or volatile substances require specialized materials like stainless steel or polymer linings, while filling machines must be explosion-proof or anti-static in certain cases.
The essence of all these sectors is the same, to convert raw materials to packaged products with consistency, accuracy and speed.
Conclusion:
The bottle on the shelf may appear to be a simple commodity, but it is the result of a very engineered process. The synchronized dance between the mixer tank and the filling machine enables the efficient production of thousands of consumer goods we use every day.
These machines can be working behind the factory doors, but we can see the effects of them everywhere in the food on our kitchen tables and in the medicine in our cabinets. These systems are also changing with the drive by industries to be more efficient, automated and environmentally friendly.
Learning the science behind mixing and filling systems not only emphasizes the significance of industrial automation but also makes us remember about the accuracy and creativity that is put into modern life to make it more convenient, safe, and connected.