With the further development of the packing technologies, the location of the engineers is not only in the realm of containment, but also in the areas of shelf life extension, maintenance of the product integrity and optimization of the production process. Metal-based containers, especially those with oblong tin can lids, have remained vital across industries due to their durability and product compatibility.
Meanwhile, sealing solutions like the aluminum foil sealing machine are becoming increasingly precise, hygienic, and automated.
These three innovations, in combination, are a combination of form and functionality- the marriage of mechanical engineering and materials science. How therefore do these components work and why are they as important as they still are in the modern day package systems? Now, let us get more into the science and the machineries that make this branch of the packaging industry.
Oblong Tin Can Lids: Structure, Material, and Utility
Oblong tin can lids are a specialized form of closure designed to fit rectangular or oval-shaped tin containers. They find application in the food industry (e.g. fish, meat spreads and confectionery) and in industry (e.g. adhesives or polish). The oblong shape is not only cosmetic: it makes shelf use, storing and portioning of the product more efficient.
As a material science view, these lids are manufactured out of tin-plated steel or aluminum. The coating is made of tin, which gives corrosion resistance and the base metal is made of metal which gives structural strength. The packaging styles of lids differ depending on the type of product packaged, with simple-opening tabs, peelable membranes or compound-coated sealing rims being some of the characteristics that make the packaging air-tight.
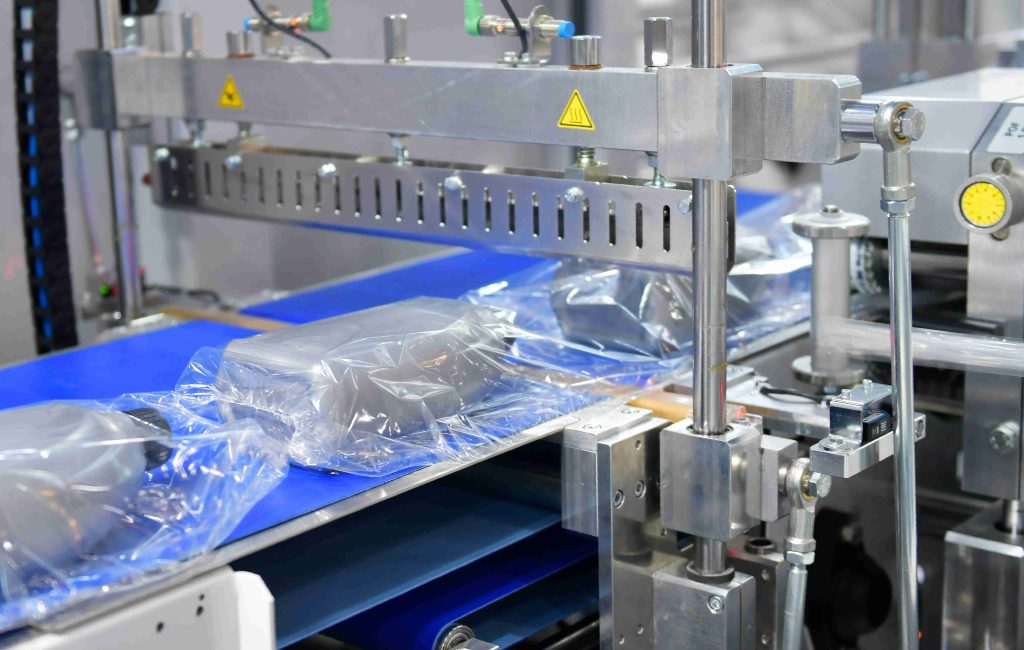
Manufacturing of these lids requires accuracy. The shape should be snug so that there is no gap or warping and this is done by progressive stamping and deep drawing. The geometry also determines the sealing process- is it crimp based, heat seal based or compound seal based.
Aluminum Foil Sealing Machine: Mechanism and Application Scope
An aluminum foil sealing machine is a high-performance device used to seal containers with a layer of aluminum foil—ensuring tamper resistance, leak prevention, and extended shelf life. These robots are quite evident in the food, pharmaceutical and cosmetic industries where hygiene and preservation are utmost.
Induction heating or direct thermal contact is normally applied to the sealing process. In induction sealing a conductive layer in the aluminum foil is made hot by an electromagnetic field, which activates the polymer adhesive to stick the foil to the container rim. The foil is the only object subjected to heating- the product remains intact and of its quality.
These machines are compatible with a variety of container materials, including plastic, glass, and metal. They can also accommodate different lid types and container geometries—such as round jars, square tins, and even oblong tin cans.
Modern aluminum foil sealing machines feature automated alignment systems, pressure-controlled sealing heads, and integrated rejection systems for defective seals. This level of automation ensures high sealing accuracy while minimizing waste.
Installing such machines into a production line helps businesses improve product safety, meet regulatory standards, and increase throughput without compromising on packaging quality.
Integration in Production Lines: Matching Lids with Foil Seals
The integration of oblong tin can lids with aluminum foil sealing machines represents a fusion of mechanical design and thermal sealing technologies. In some forms of packaging the aluminum foil is used as an inner liner-it is sealed against the container and then the metal lid is applied. This two-layered covering provides an excellent safeguard against oxidation, moisture and microbial contamination.
The packaging lines are developed in such a way that the foil seal and lid application follows each other. For example, a container may first pass through the aluminum foil sealing machine, where the foil membrane is sealed to the product. This is swiftly followed by the crimping or snapping of the oblong tin can lid through a mechanical mechanism with the help of a separate capping or closing unit.
There must be precision synchronization of these stages. Speed of the conveyors as well as indexing of the containers together with the placement of the lid should be precise to avoid contamination or wrong application. Advanced plants have systems with coordination between sealing and lidding activities using PLCs and the result is consistent.
It is a flexible packaging design, too, as this modular approach enables. Besides the security advantages of foil sealing, brands can provide tamper-evident features, resealable lids or fancy looking outer caps.
Material Science Behind Metal Lids and Foil Layers:
Both oblong tin can lids and aluminum foil layers are engineered with specific barrier properties to protect the product inside. The important point is knowing the composition and layering of the material to maximise their combined performance.
Oblong tin can lids, usually made from electrolytic tinplate or aluminum, offer strong mechanical protection. Tinplate forms a corrosion resistant surface, particularly of importance with acidic food products or chemical substances. Lids frequently contain a sealing compound or gasket to maintain air-tightness without the need of any extra adhesives.
Conversely, aluminum foil in sealing lines is multi-layer laminate, which commonly consists of aluminum, PET and heat-seal polymer. The polymer makes it adhere to the container and the aluminum gives a strong oxygen and light shield. The choice of these layers depends on the temperature sensitivity of the product, the chemical content of the product as well as the shelf life that is needed.
The foil seal is also a microbial and oxygen barrier and the lid is used to seal mechanically and give space to brand. The combination provides protection and redundancy, a key aspect in the extension of the shelf life and quality of the products under varying environmental aspects.
Automation, Quality Control, and Future Developments:
The packaging automation is no longer a luxury in an ever-competitive market place. Both the oblong tin can lid application systems and aluminum foil sealing machines have evolved to meet demands for precision, speed, and traceability.
The systems today have been installed with vision sensors to identify misaligned lids or incomplete seals and reject faulty units automatically. More advanced foil sealing machines have an RFID or barcode reader to connect individual packets to production batches e.g. improving traceability and regulatory compliance.
In the future, manufacturers are looking into sustainable alternatives. As an example, recyclable sealing films and bio based liners are under test as alternatives to more traditional plastic-polymer composites. In the meantime, energy efficient induction devices are making sealing of foils less energy intensive.
There is also an increase of smart factory integration. Machines are being built to communicate with central control systems- which makes it possible to do predictive maintenance, automatic reports, and real time quality analysis.
The result? A new generation of packaging lines where aluminum foil sealing machines and oblong tin can lids are no longer passive components but intelligent contributors to performance, compliance, and sustainability.
Conclusion:
Packaging now involves precision mechanics, thermal science and materials engineering as well as containment. From the robust structure of oblong tin can lids to the advanced sealing process enabled by the aluminum foil sealing machine, every element plays a role in maintaining product integrity and consumer trust.
These are technologies that keep on changing with the demands of the market in safety, speed and sustainability. With the increasing depth of automation and the intelligent use of materials, manufacturers are getting access to potent tools to increase the efficiency of their operations and improve the product quality.
With the science of these innovations, businesses can make informed decisions that do not only affect their packaging lines, but also the experience of every end user.