Precision engineering is crucial in the rapidly developing packaging industry where the functionality and the aesthetics are combined. Whether it is food or cosmetics, industrial lubricants, and more, the packaging design does not only affect the safety of the product but the user experience and brand value as well.
Two seemingly unrelated yet fundamentally important components—cone top can lids and the aluminum foil rewinding machine—demonstrate how packaging solutions have evolved through material science and automation.
Whereas one is an important packaging component in can based systems, the other is an important machine component which processes one of the most versatile materials in the industry, aluminum foil. The article will discuss how these elements lead to smarter, more efficient and safe packaging in the current manufacturing environment.
The Importance of Specialized Packaging Components in Industry:
Packaging is no longer containment. It is conservation, accessibility by the users, compliance with the regulations, and aesthetic value. Each industry; whether it is food and beverage, pharmaceuticals, chemicals or household goods, needs unique packaging solutions based on the specific needs of the products.
Expansion of consumer knowledge, sustainability issues, and the need to increase shelf-life have turned packaging into a science on its own. Components such as cone top can lids, which offer ergonomic pouring and secure sealing, are engineered not just for form but also for superior function.
On the same note, the manufacturing of the aluminum foil behind the scenes by the use of sophisticated machines guarantees that they come in the best form, crease-free, homogeneous, or flawless. They may be small in size but these components are big contributors to large-scale performance and safety of products.
What Are Cone Top Can Lids and Where Are They Used?
Cone top can lids are a distinct style of can closure that taper upward into a narrow opening—much like a funnel. The practicality of this design is very high: it can be poured with precision, has fewer spills and in many cases, such containers are resealable, such as a screw cap. These lids are cone shaped and hence are suitable when working with liquids, aerosols, oils or viscous materials.
Cone top lids are frequently used in motor oils, solvents, beverages and specialty foods, where there is a need to control dispensing, but also maintain structural integrity. Such lids are typically manufactured of tinplate or aluminum and are intended to resist internal pressure and provide tamper evidence and corrosion resistance.
They are of branding value as well because they can be custom printed or embossed. The lid region can be used by companies to print color branding, instructions or even promotion.
Aluminum Foil Rewinding Machines: Behind-the-Scenes of Foil Processing
While cone top can lids are visible to consumers, the aluminum foil rewinding machine operates silently in the background of many manufacturing facilities. This machine is important in that it rolls bulk foil rolls into smaller size rolls of precise length ready to be used or packaged further.
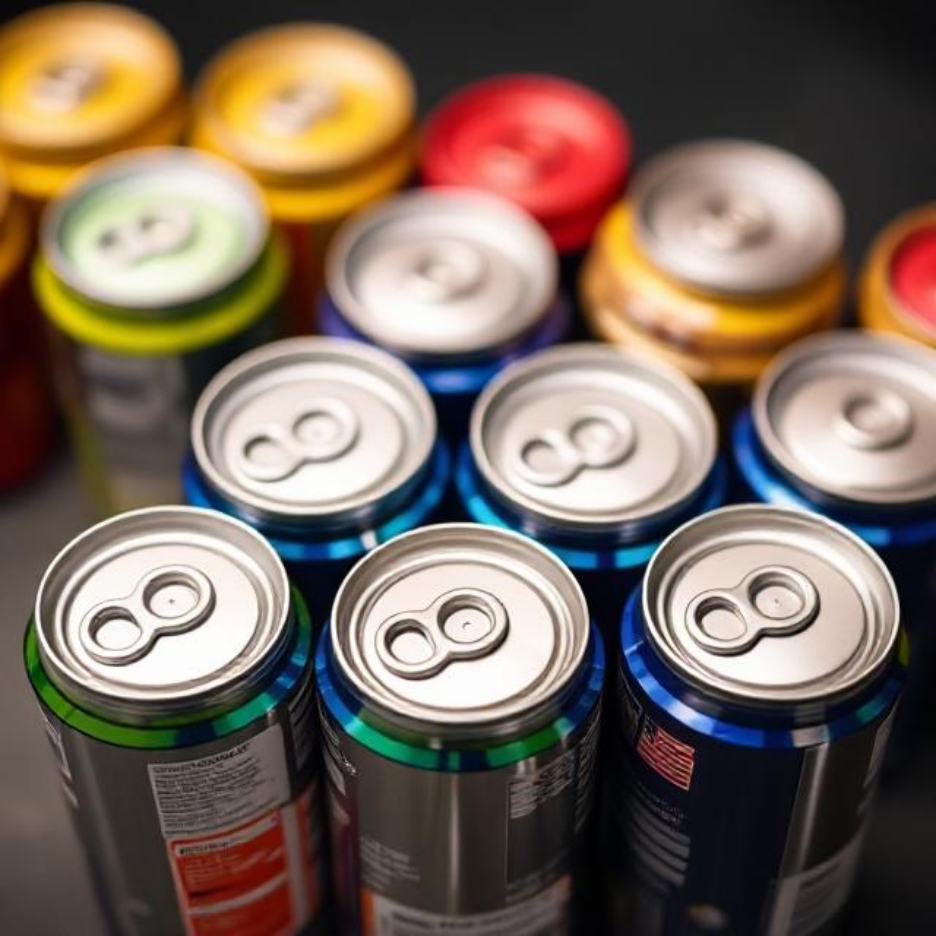
The machine starts by feeding a huge jumbo roll of aluminum foil. The foil is reeled onto smaller cores with controlled tension synchronization, blade cutting and spindle driven rewinding. The output is standard, wound tightly rolls that are accurately measured in length, width and thickness.
Modern aluminum foil rewinding machines are equipped with features such as:
- Automatic roll changeover to improve efficiency
- Precision tension control to avoid tearing or stretching
- Laser or blade cutting systems for clean edges
- Programmable logic controllers (PLCs) for repeatable operations
These machines are used in many different applications, in foodservice and household kitchen foils through to insulation, pharmaceuticals and laminates. A properly tuned rewinding machine will keep the foil with its barrier characteristics–needed to keep food fresh, to package drugs, or to line composite packaging materials.
How Engineering Precision Enhances Packaging Efficiency?
Whether it’s the accurate threading of an aluminum foil rewinding machine or the press-fit of cone top can lids, precision is the foundation of modern packaging operations. The incorrect sizing of the lids may cause leakage or contamination of the products, and the improper winding of the foil may cause the wastage of materials and inefficiency in downstream processing.
The current packaging is largely automated to enable it to cope with the increasing demand and still provide quality. High-speed lines rely on standard parts which fit, seal and work in a precise manner. This involves tolerances in microns particularly in materials that are only a few micrometers thick such as aluminum foil.
Where cone top lids are used, dimensional consistency would make them compatible with filling lines and sealing machines. In the case of aluminum foil, the rewound rolls should unroll freely, without twisting, distortion or misregistration in subsequent packaging devices. In both of them, minor engineering variations may lead to downtimes, loss of products, and increased production costs.
Material Innovation in Lid and Foil Applications:
Innovations in the materials have also improved the performance of cone lids and foil products. Lightweight but strong alloys have recently been used in the production of lids in order to minimize the use of material without compromising the strength. Acidic or volatile contents are now standard in lids with anti-corrosion coating.
In the case of aluminum foil, lamination methods have enabled the manufacturers to mix the metal with other polymers or paper to come up with hybrid materials that exhibit the properties of both barrier and flexibility. Recyclable and biodegradable coating is under development in order to achieve global sustainability targets.
Simple packaging materials are becoming multi-functional, such as the embossed foil to help detect tampering or anti-microbial coating on the lid of a food to help ensure food safety. These innovations support the point that packaging is emerging as a very technical and solution-oriented enterprise, as opposed to a commodity.
Automation and Quality Control in Packaging Equipment:
Both cone top can lid production and aluminum foil rewinding machines are benefitting from advances in automation and quality monitoring. In making the lids, the high-speed stamping and trimming lines are currently installed with vision systems that identify defects like cracks, dents, or inconsistencies in the coatings.
Tension sensors, optical edge detection and intelligent alignment tools are all used in foil rewinding machines so that every roll is to precise customer specifications. Such automated systems minimize the use of manual inspection, accelerate throughput, and allow traceability, which is becoming more and more significant in regulated markets such as food and pharma.
Automation does not only enhance precision but also aid in scalability. With the rise in demand, the packaging facilities are able to produce more without compromising the quality- a win-win situation to both the producers and the consumers.
Conclusion:
The issue of packaging is both an engineering and marketing activity in the current competitive and quality conscious markets. Components like cone top can lids enhance usability and safety, while machinery like the aluminum foil rewinding machine ensures material readiness and efficiency in large-scale production.
The combined efforts demonstrate how accuracy, creativity and material science can come together to satisfy the growing needs of contemporary packaging. With technologies that are constantly developed, we may anticipate even more intelligent, more sustainable, and more responsive solutions to define the future of packaging design.