In this era of heightened environmental awareness, plastic is no longer merely an industrial material but has become the focus of public opinion. From Marine pollution to “white garbage”, it has almost become a synonym for environmental problems. Plastic, in fact, is not inherently a “sinner”. The real question is – where does it go after being used once? Disposable, discarded at will, non-biodegradable… The reason why plastic is “demonized” is that we do not design a second life for it after using it.
The good news is that more and more forward-looking manufacturing enterprises have realized this. They no longer simply regard plastic waste as “garbage”, but re-incorporate it into the resource system as a “raw material repository” for sustainable manufacturing. From the recycling and reuse of waste plastics to the establishment of zero-waste factories, enterprises are redefining the life cycle of plastics.
Behind all these changes, the support of advanced recycling equipment and systematic recycling logic is indispensable. Re-understanding plastic and redesigning its destination is an important step for us towards a green future.
Unseen industrial plastic waste: The true mainstay of recycling
TThe recycling we see in our daily life is mainly plastic bottles and plastic bags, but in fact, the real main force of plastic recycling comes from factories. For instance, in the production process of car body protective films, the amount of plastic waste generated daily on the production line, including the scraps of each injection molded part, the by-products of each extruded board, every defective product, and the leftover materials from trimming, is astonishing.
Although this type of industrial plastic waste has high cleanliness and a single composition, making it suitable for reuse, it shares a common problem: it is too large in size to be directly recycled and processed. Therefore, to take the first step in recycling, it is necessary to “crush” it first.
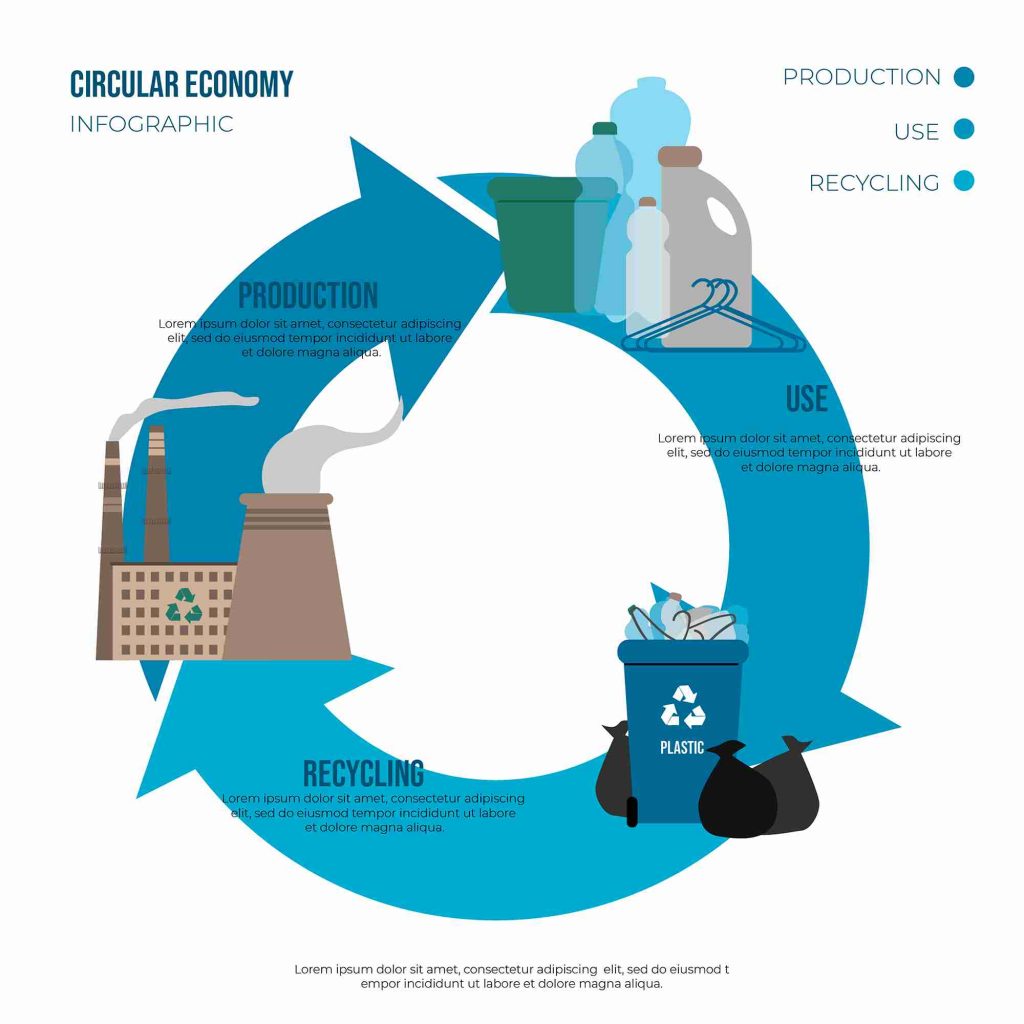
Breaking: The First threshold to open the plastic cycle
You can’t handle the things that you can’t fit into the machine. Waste materials in industrial production are often heavy, hard and even oversized. Not only are they troublesome to transport, but they are also very likely to clog recycling equipment and even cause equipment malfunctions.
Therefore, Plastic Material Waste Crushers have become indispensable equipment. It is not merely about “smashing” plastic. Its true significance lies in:
Crush the bulky waste materials uniformly into particles of controllable size;
– Provide stable and qualified raw materials for subsequent processes such as cleaning, melting, and re-granulation;
Avoid the mixture and cross-contamination of raw materials;
Improve reproduction efficiency and save labor and storage space;
– Achieve immediate processing on the production site without the need for long-term accumulation or transportation outside.
The “intermediate link” that is hidden in the production line but crucial
Modern manufacturing enterprises are increasingly inclined to “internalize” waste recycling, that is, to complete the immediate processing and reuse of plastic waste within the production process. Compared with the traditional centralized collection and subsequent transportation for recycling, this approach not only significantly enhances the processing efficiency but also effectively reduces the space pressure and management costs of temporary waste storage.
In many plastic processing workshops, we can see a medium-sized but powerful crushing equipment. It is neither noisy nor takes up too much space, but its role is of vital importance. When the equipment is in operation, it will automatically receive waste edge materials, substandard products or residual materials from the production line, without the need for manual sorting or additional transportation.
Through the built-in cutting system, these plastic wastes are quickly crushed into granular or flaky scraps. These crushed materials are directly recycled to the raw material warehouse or reprocessing unit through the feeding system, achieving a true closed-loop utilization. The entire process hardly interferes with the main line production and can even achieve unmanned continuous operation.
It is widely applied and almost covers all plastic processing industries
The application scope of Plastic Material Waste Crushers is very wide, including but not limited to:
– Packaging industry: Trimming of soft and hard packaging, crushing and reuse of film materials;
– Automotive parts: Processing of large injection-molded parts (such as bumpers, center consoles);
– Electrical appliance housing: ABS/PC plastic for the outer shell, inner liner, etc. of electronic products;
– Medical devices: Pre-treatment of disposable plastic products before recycling;
Textile industry: Polyester fiber scraps, spinneret shearing and blanking treatment;
– Building materials and plastics: Recycling and reuse of PVC pipe scraps and corrugated board offcuts.
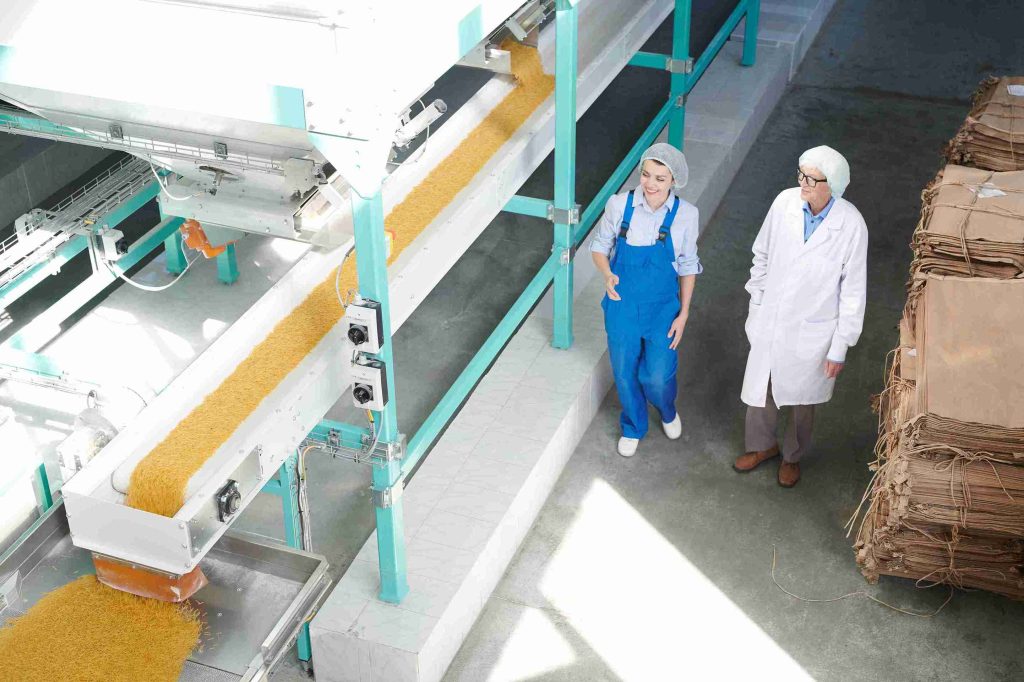
Policy-driven and compliance pressure: Environmental protection is not an option but a standard
Many countries and regions around the world have successively implemented the Extended Responsibility System for Plastics (EPR), requiring manufacturing enterprises to be responsible for the entire life cycle of their products, including recycling and disposal.
Having an independent and efficient waste crushing system means that an enterprise can:
– Increase the internal recovery rate and reduce the reliance on external entrusted processing;
Meet the government’s environmental protection compliance requirements;
– Improve ESG scores to enhance the competitiveness of enterprises in external financing or listing;
Reduce the cost of transporting and stacking waste materials, and enhance the safety and cleanliness of the factory area.
Conclusion
Fragmentation is plastic, but it is also a breakthrough point for the future.
If “green manufacturing” is a hardcore yet elegant system upgrade, then plastic crushing equipment is the underestimated but absolutely crucial unsung hero behind the scenes. It may not be as cool as a robotic arm, but it is the “breakthrough point” for all closed-loop manufacturing.
Don’t underestimate the two words “broken”. The transformation of plastic from waste to new resources relies on a series of stable, efficient and intelligent collaborative crushing equipment. They silently carry the “second life” of manufacturing, reshaping the value of plastics with precision and efficiency, and supporting the underlying logic of moving from “linear production” to “recycling and regeneration”.
This is not only the “posture” of environmental protection, but also the “posture” of industrial upgrading. When “fragmentation” is no longer a synonym for inefficiency but a new starting point for resource optimization, data empowerment and intelligent manufacturing, crushing equipment may still remain low-key, but they are redefining the essence of manufacturing – more environmentally friendly, smarter and more resilient.
So, don’t wait until you are eliminated to remember the importance of being “broken”. Taking the initiative to understand and make plans is the true way to master the future.