Specifics and sanitation are not luxuries but necessities in the fields involving non-negotiability of the safety of the products offered: in food and beverages, in pharmaceuticals. A wrong turn with either cleanliness or accuracy of filling may result in product recalls, endangerment, and the loss of brand trust that can never be retracted.
With time, the demands of the consumer as well as the regulatory standards continue to increase, thus manufacturers have resorted to high-tech automated processes to ensure that quality does not fall short. In this pursuit, two components stand out: the filling machine, which governs the accuracy of dosing, and the FDA & Sanitation pump, responsible for safe fluid transfer without contamination.
This article explains the interaction of these technologies to provide results that are high performance and yet sanitary compliant. We shall equally look into clean-in-place systems, system integration, and principles of design that facilitate effective production without contamination in the sophisticated facilities.
Filling Machines: Core Components of Modern Production Lines
The filling machine is a central component in any automated production line, playing a critical role in ensuring product consistency, packaging speed, and operational efficiency. Whether it is bottled water, pharmaceutical syrups or granules, these machines can process a variety of liquids, pastes and granules and fill them into containers with a high level of speed and accuracy.
Modern filling machines are built with programmable controls, adjustable nozzles, and sensors that reduce waste and overflow. Depending on the viscosity of the product and the type of container, volumetric filling, gravimetric systems and piston-based models can be chosen. Few sophisticated machines also have automatic bottle alignment, capping, and labeling to automate end to end processes.
In sensitive industries such as food and pharmaceuticals, sanitation is a major requirement. The materials that are utilized in the construction of machines, which is usually stainless steel, should be resistant to corrosion and bacterial growth. Also, disassembly and smooth finishing of the surfaces facilitate a regular cleaning cycle and avoid the accumulation of residues.
Downtime during changeovers is another challenge that filling machines help address. The modular designs and the programmable settings enable a rapid change of the product or bottle size with minimal intervention which is essential in high-mix, high-volume manufacturing environments.
The Importance of FDA & Sanitation Pumps in Sensitive Fluid Handling:
In applications where hygiene is critical, the role of the FDA & Sanitation pump cannot be overstated. These pumps are specially designed and approved to pump food, dairy, pharmaceutical, and cosmetic products, where even the slightest contamination can make a significant impact.
An FDA & Sanitation pump is constructed with materials that meet FDA standards, often including food-grade stainless steel, PTFE, and elastomers that resist chemical degradation. This pump is designed with smooth, crevice-free surfaces. Because such design can help in avoiding microbial growth and full drainability during clean-in-place (CIP) operations.
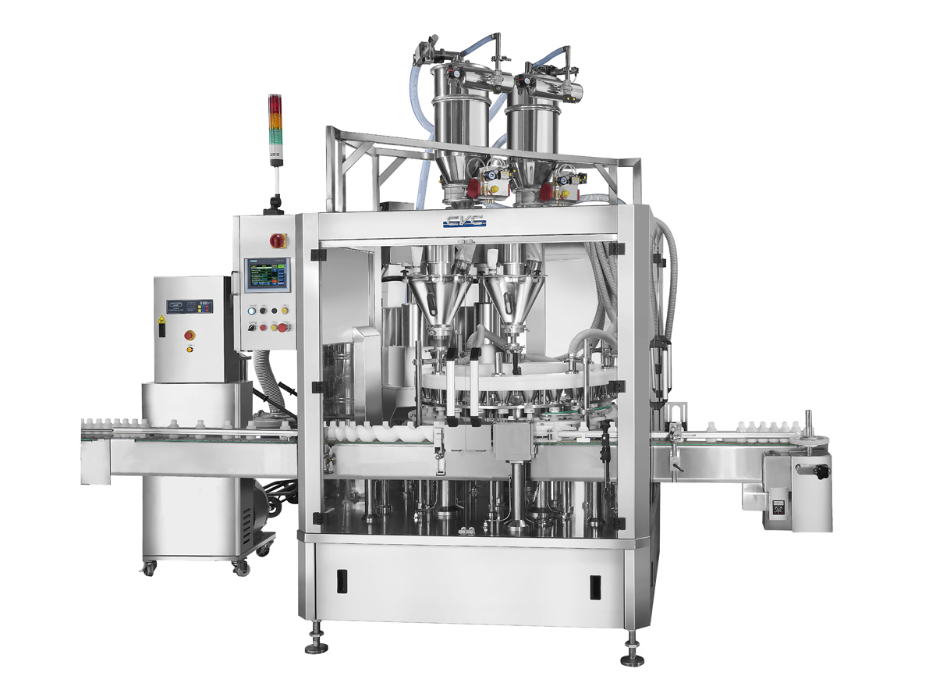
Sanitation pumps are of various types, namely, diaphragm pumps, peristaltic pumps, and rotary lobe pumps. All are chosen depending on the viscosity, shear sensitivity and particulate matter of the product being transferred. As an example, a rotary lobe pump would be suitable in viscous fluids such as a sauce or an ointment, whereas a peristaltic pump might be better for a sterile pharmaceutical transfer.
These pumps are frequently combined with flow meters, pressure sensors and automated control systems to maintain constant flow rates. Besides maintaining the flow rate, such pumps also minimize pulsation and precise volume delivery to subsequent operations such as filling or mixing. Others also have self-priming and dry-run protection to reduce risk of operation.
What makes FDA & Sanitation pumps indispensable is their dual promise.
- Product integrity
- Regulatory compliance.
In industries where public safety and consumer trust are paramount, these pumps serve as the gatekeepers of clean, controlled fluid movement within the production line.
How Clean-in-Place (CIP) and Sanitary Design Prevent Contamination?
Hygiene in production environments goes beyond a periodic cleaning. It entails systematic, repeatable, as well as validated sanitation processes. Clean-in-Place (CIP) systems are a cornerstone of sanitary manufacturing, enabling internal cleaning of pipes, pumps, tanks, and filling machines without disassembly.
CIP systems pump cleaning solutions, usually water, acid, alkali and sanitizers, around the processing line at regulated temperatures and flow rates. This is an automated process where all contact surfaces with the product are well sterilized to minimize microbial risks and avoid residue of the product.
Sanitary equipment design is necessary in line with CIP. Both FDA & Sanitation pumps and filling machines are built with hygienic principles in mind: minimal dead zones, self-draining geometries, and corrosion-resistant materials. As an example, weld seams should be polished, gaskets are preferably FDA compliant and fittings do not trap residues.
One of the greatest benefits of the CIP systems is that they are efficient. They save manual work, water and chemicals, and they do not have downtimes between batches of production. The process is furthermore more reliable and traceable when combined with programmable logic controllers (PLCs) allowing compliance with Good Manufacturing Practices (GMP), HACCP and FDA audit requirements.
CIP and hygienic design are a formidable combination of protection against contamination. They ensure that the product moves from FDA & Sanitation pump to filling machine in a clean, closed-loop environment—free from the risks that threaten both product quality and consumer health.
System Integration: Ensuring Smooth Workflow Between Pumps and Filling Units
For an automated filling system to operate at peak performance, seamless integration between pumps and filling machines is crucial. It is not just sufficient that every part is effective in its own regard, but that they are able to communicate and cooperate throughout the manufacturing process.
FDA & Sanitation pumps feed product fluid to filling machines, where accurate metering and container filling take place. A pump that pumps too fast will overflow the filling chamber; too slow and the process will become a bottleneck. This is why smart flow control is essential, either via sensors, variable frequency drives (VFDs) or PLC coordination.
The synchronization is especially critical in fast-running bottling lines or drug filling stations where the accuracy of dosage and the line speed have to be exactly matched. If fluid pressure or viscosity fluctuates, the filling machine may overfill or underfill containers, affecting both yield and compliance.
Conclusion:
Cleanliness and precision are not just technical objectives in the high-stakes manufacturing world, but the basis of trust. The quality of a product and the integrity of a brand can be spoiled by a drop of contamination or a wrong fill. This is the reason why businesses have to invest in the appropriate technologies.
With the combined power of a well-calibrated filling machine and a certified FDA & Sanitation pump, manufacturers can ensure that every bottle, vial, or pouch meets the highest standards of hygiene and accuracy. Add in clean-in-place systems, intelligent integration, and hygienic design and you have a comprehensive environment of safe, efficient production.