In an age where craftsmanship and precision are key to industrial prowess, the union between high-powered industrial tools and craftsman-like textile design is changing the standards of packaging. At the forefront of this revolution lies the sealing machine, a cornerstone of high-speed production lines, and the humble yet versatile custom felt bag, a symbol of sustainable, bespoke packaging.
This article examines the ways in which the latest technologies in sealing have been fitted to the peculiarities of felt so that manufacturers could offer eco-friendly, durable, and eye-catching packaging options.
Through material science, machine operation and emerging trends, the readers will have an insight on how sealing processes enhance both the functions and the forms in the current competitive market.
What Are Custom Felt Bags and Why Are They Popular?
Custom felt bags have surged in popularity across fashion, retail, and corporate gifting sectors thanks to their tactile appeal, environmental credentials, and design flexibility. Felt can be cut, molded and decorated easily and is made mainly of wool or recycled plastic fibers and provides a soft, sturdy substrate. Felt is more matte, with softer tones, which is why brands prefer this material because it creates an impression of quality.
In addition to being aesthetically pleasing, felt also has terrific insulating and protective qualities, and is thus perfectly suited to the packaging of fragile products, whether electronics or artisanal products. As companies seek to distinguish themselves, a custom felt bag serves as both a functional container and a marketing tool, providing a tactile brand experience that paper or plastic cannot match. As the interest in sustainability continues to grow, the recyclability and biodegradability of felt add further to its advantage, making custom felt packaging one of the best options in the business of companies focusing on sustainability.
Material Science Behind Felt and Its Suitability for Sealing Processes:
Felt is a non-woven fabric, which is made through matting, condensing, and pressing fiber together. Its structure is not interlaced, like that of woven fabrics, but, when subjected to heat, moisture and pressure, microscopic barbs on the wool fibers, or chemically treated synthetic fibers, are caught together. This special blend provides strong tensile strength, dimensional stability and it is also resistant to fraying.
These characteristics make felt compatible with various sealing machine technologies. The porous quality of felt enables heat to pass through to bond fibers together without melting, maintaining integrity of the bag. Sealing can be enhanced prior to treatment by moisture resistance treatment and flame-retardant finishes. Besides, the uniform thickness of felt guarantees the uniformity of the sealing depths, and the flexibility of felt can support the advanced sealing heads, hot-bar systems as well as ultrasonic welders.
Being aware of these characteristics of materials is critical to engineers and designers who want to maximize sealing parameters of temperature, dwell time and pressure to obtain durable seals, with no degradation of aesthetic qualities of custom felt packaging.
How Sealing Machines Work: From Heat to Ultrasonic Precision?
Modern sealing machines fall into two main categories:
- Thermal bar sealers
- Ultrasonic welders.
Thermal bar sealers use heated platens, which are covered with non-stick Teflon to press and fuse surface fibers, creating a permanent seal when cooled. This process is good with synthetic mixes, offering powerful, constant seals suited to closure of bags and ornamental edges.
Ultrasonic sealing machines, on the other hand, use high‑frequency vibrations to generate localized heat through friction. Ultrasonic horn uses pressure and oscillation between 20 kHz and 40 kHz in order to produce interlocking of fibers without bulk heating. Advantages are reduced cycle times, less energy and no use of glue or thread. Felt is especially suitable for ultrasonic sealing because it does not do much thermal damage and retains texture.
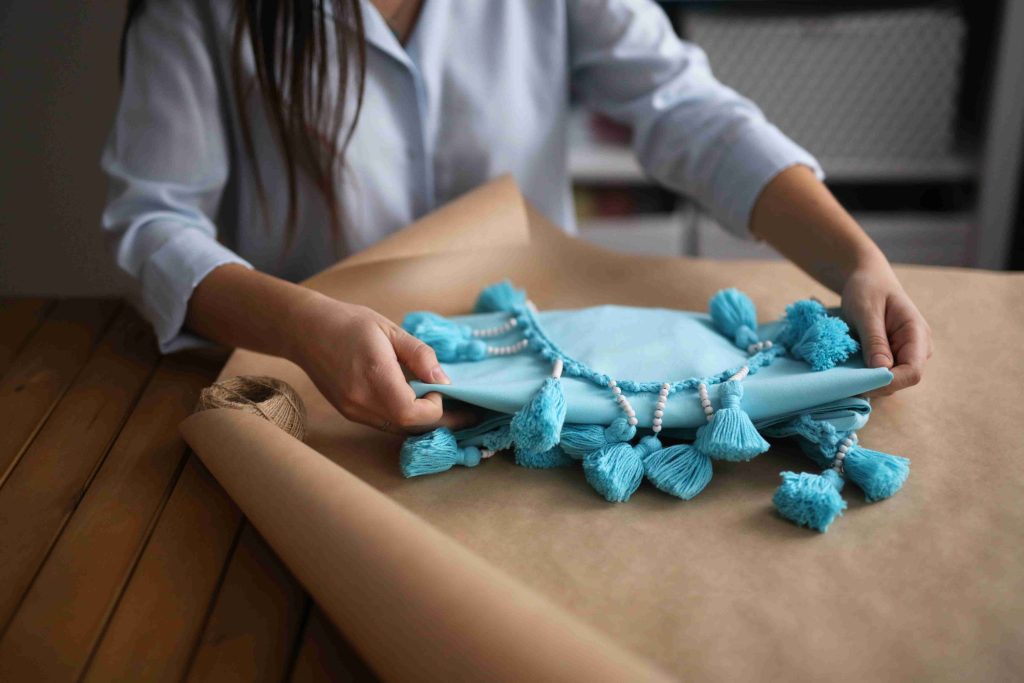
The two technologies are easily implemented on an automated production line. Programmable logic controllers (PLCs) regulate sealing parameters, while robotic or conveyor systems deliver custom felt bags to the sealing head. This creates a very accurate, repetitive process, which is able to satisfy the high volume requirements of modern manufacturing.
Adapting Sealing Machines for Custom Felt Bag Production:
Transitioning from plastic film to textile substrates like felt requires thoughtful adaptation of sealing machinery. To begin with, engineers control temperature profiles: hot-bar sealers are set to lower temperatures (120-160 C) to avoid fiber scorch, and ultrasonic systems adjust amplitude and pressure to suit the density of felt. Horn geometry and anvil plates will also spread the force uniformly over the surface of the bag to provide uniform welds without damaging the nap.
The speed of conveyors and dwell time is optimized to enable adequate energy transfer and sensors, e.g. infrared thermometers, are used to monitor seal integrity in real time. For bags with multiple layers (e.g., felt lined with fabric backing), the sealing machine must synchronize its cycle to create full‑penetration seals. Also, gusset tooling and shaped cutout tooling can be incorporated into the sealing head and allow on-the-fly customization directly on the production line. These adaptations empower manufacturers to produce custom felt bags at scale, combining artisanal aesthetics with industrial precision.
Benefits of Using Sealing Machines in Felt Bag Manufacturing:
Using a sealing machine in felt bag production offers several advantages. Some are listed hereunder:
- Speed & Consistency: Automated cycles yield hundreds of units per hour with identical seal quality.
- Strength: Seals created via heat or ultrasonic welding rival stitched seams. This ensures durable packaging.
- Clean Finish: Eliminates loose threads and adhesive residues, preserving the minimalist appeal of felt.
- Cost Efficiency: Reduces labor and material waste compared to traditional sewing or gluing methods.
- Versatility: Compatible with a range of felt thicknesses, blends, and post‑sealing treatments.
Together, these benefits make sealing technologies indispensable for brands. Such machines are important for those companies that seek to scale high‑end custom felt bag offerings without sacrificing craftsmanship.
Customization Trends: Branding, Embossing, and Precision Sealing for Felt Bags:
The concept of customization continues to fuel the packaging innovation. Brands increasingly leverage sealing machines to incorporate:
- Embossed Logos: Specialized sealing dies imprint brand marks directly on felt surfaces.
- Color‑Contrast Seals: Integrating colored thermal tapes or ultrasonic seams for visual accents.
- Smart Tags: Embedding RFID or NFC labels within sealed layers for supply‑chain tracking.
- Edge Profiling: Precision cutting and sealing create decorative scallops, waves, or laser‑etched patterns.
Conclusion:
The integration of advanced sealing machines with custom felt bag production exemplifies how precision engineering can amplify artisanal design. The manufacturers are redefining packaging quality and brand engagement through material science, adaptive machinery and sustainability-inspired innovations. The future of textile packaging will no doubt be determined by the convergence of sealing technology and felt craftsmanship as the demand rises in order to find a unique, environmentally friendly solution.