With stricter environmental rules, unpredictable raw material prices, and the constant push for smarter manufacturing, factories today have a lot on their plates. Amid all this noise, one question keeps popping up: what’s the smartest way to deal with scrap metal? It piles up—steel offcuts, aluminum trimmings, dented components that didn’t pass QC. You can’t ignore it, but you also can’t afford to let it eat up space, profits, or peace of mind. The good news? Scrap metal holds hidden value—you’re the one who can unlock it.
More manufacturers now realize: with smart handling, waste can become a business asset.
On-site shredding, clean separation, and smooth workflows make all the difference.
The result? Less clutter, lower costs, and better profit margins.
Plus, sustainability earns you extra credibility and brand points.
Today, recycling isn’t the challenge — smart and fast recycling is.
It’s about efficiency, impact, and protecting your bottom line.
Scrap Metal: An Undervalued Resource
From cuttings and trimmings to outdated components and rejected prototypes, metal waste piles up fast in manufacturing environments. And while it may look like junk on the surface, don’t be fooled—materials like copper, aluminum, and stainless steel hold serious residual value. The problem? If left unmanaged, that value slips away. Stack those parts in a corner too long, and you’re not just wasting space—you’re risking oxidation, contamination, and a whole lot of lost potential. And let’s face it, cluttered workspaces don’t do anyone any favors.
The good news is: with a bit of planning and the right processing tools in place, all that scrap can be turned into a profitable, clean, and sustainable resource stream. In fact, treating metal waste as a resource—rather than an afterthought—is quickly becoming a hallmark of modern, efficient manufacturing operations. It’s not about throwing it away—it’s about throwing it forward, into something better.
The Shift Toward Integrated Metal Recycling
Forward-looking manufacturers no longer see metal recycling as a task for “later” or “someone else.” It’s not just a side project—it’s part of the core game plan.These companies now weave recycling into daily operations and resource strategies.
It’s no longer an afterthought but part of how they work.
Rather than stockpiling scrap metal for haulers, they handle it themselves.
By bringing recycling in-house, they stay efficient and in control.
That means investing in pre-treatment and recovery systems that are integrated right into the production line—shredding, sorting, and prepping materials while the machines are still humming. The result? Faster turnaround, lower handling costs, better material quality, and real-time visibility into what’s being recovered. It’s not just about being green—though that helps with ESG goals—it’s about being smart, efficient, and ready to capture every bit of value from what used to be considered waste. In modern factories, recycling isn’t the afterthought. It’s the advantage.
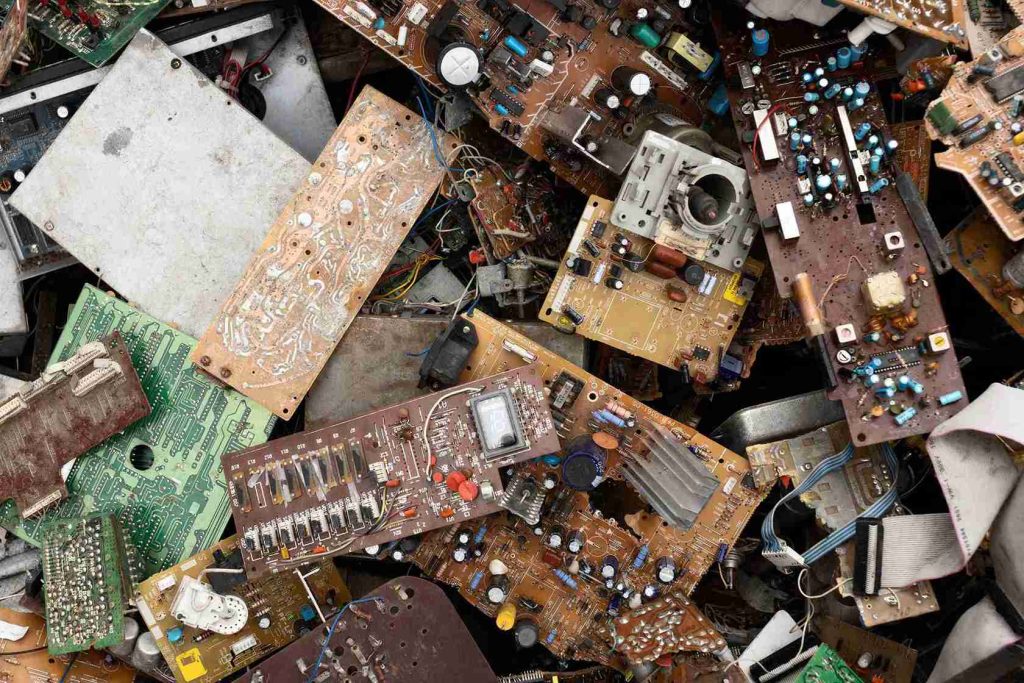
The Often Overlooked Power of Shredding
Recycling isn’t just about collecting and weighing metal. It’s about maximizing its value and usability. That’s where shredding comes in.
In modern, high-efficiency operations, metal shredders reduce bulky or irregular waste into compact, manageable fragments. This step increases ease of storage, improves transport efficiency, and allows for better sorting by material type—ultimately improving resale or reuse value.
According to some recyclers, shredded metal can command 15%–30% higher prices than unprocessed waste.
Automotive Metal Parts: A High-Value Recycling Scenario
The automotive sector is a prime example of high-volume, high-value metal recycling. During manufacturing and repair, components like door panels, stamped trims, engine brackets, and steel arms often become scrap. These parts are bulky and structurally complex, making them difficult to handle without initial processing.
What’s more, automotive metal parts often contain mixed materials—aluminum alloys, stainless steel, carbon steel—requiring high-purity sorting for maximum reuse.
Some advanced factories now deploy specialized shredding systems for automotive scrap at the production line, achieving automated intake, fragmentation, and classification. This reduces manual handling, cuts storage needs, and improves internal recycling efficiency.
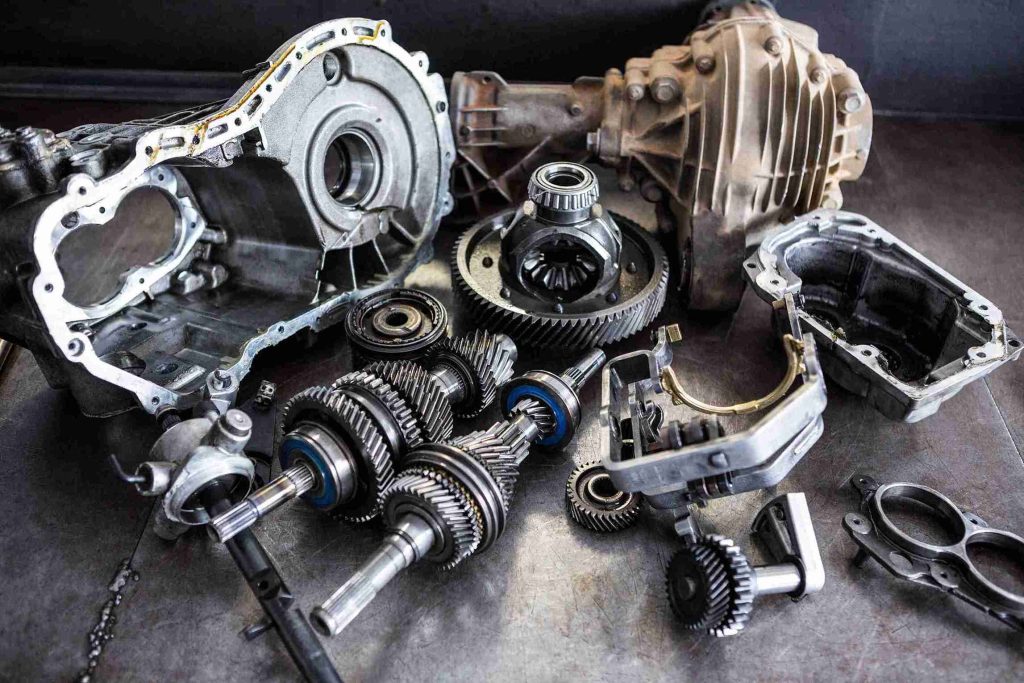
From Cost Control to Brand Value
Beyond the direct savings, properly managing scrap metal is becoming a reputational asset. In bidding for international contracts or public sector projects, traceable waste management and recycling data are increasingly required.
An internal recycling system not only meets compliance—it enhances a company’s environmental credibility and operational transparency.
Small Machines, Big Impact
Many facilities are now integrating compact metal shredding equipment into their existing layouts. These machines are:
– Modular and space-efficient
– Compatible with diverse metal types
– Equipped with safety and remote monitoring features
– Easy to clean and maintain
Though small, they are critical components in high-value recycling chains.
Conclusion
Metal recycling isn’t just about ticking off regulatory boxes anymore. It’s fast becoming a real competitive advantage. In today’s era of low-carbon mandates and lean manufacturing, the businesses that win aren’t just those that make great products—they’re the ones that manage resources smartly, efficiently, and sustainably. Companies that build closed-loop recycling systems aren’t just saving money—they’re building resilience, improving traceability, and future-proofing their operations.
And here’s the thing: this kind of transformation doesn’t always start with a massive overhaul. Sometimes, it begins with one compact, quietly running machine tucked away in the corner of a production floor—shredding, sorting, and setting in motion a much bigger shift. It may not be flashy, but its impact ripples through the entire operation. In the race toward smarter manufacturing, it’s not just about who moves fastest—it’s about who builds smarter systems from the ground up. And that starts, quite often, with a simple yet powerful decision: to turn waste into value, in-house.